Optimizing warehouse operations has become a strategic imperative for sustained success in the modern business landscape.
Key Performance Indicators (KPIs) play a pivotal role in this pursuit, offering a comprehensive framework to measure, analyze, and enhance the efficiency and performance of warehouse facilities.
According to the 2023 Third-Party Logistics (3PL) Warehouse Benchmark Report, the challenges faced by 3PLs in 2023, including economic fluctuations and lower-than-expected e-commerce growth, highlight the critical need for strategic decision-making.
The best-performing 3PLs are focusing on metrics, particularly KPIs, to navigate these challenges. The emphasis on diversification, resilience, and automation aligns with the data-driven approach facilitated by these critical measurements.
This article will shed light on the significance, selection process, and effective implementation strategies of warehouse KPIs. By the end of this exploration, you’ll not only understand the vital role of warehouse KPIs but also gain insights into leveraging them for tangible improvements in productivity.
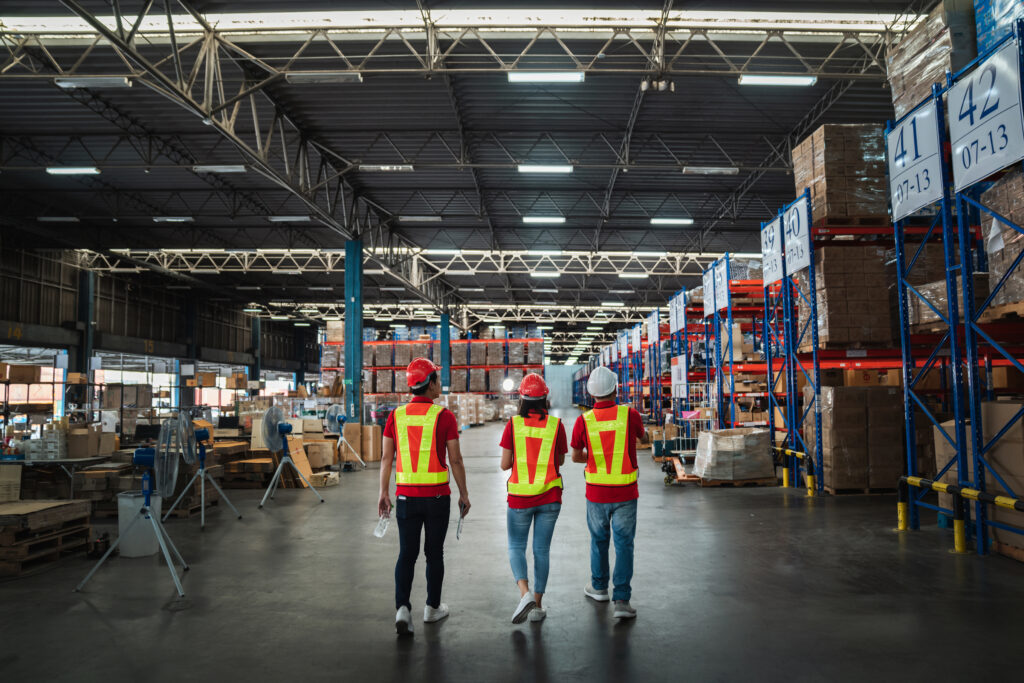
Exploring the Impact of KPIs
Warehouse KPIs act as a report card, systematically assessing how well processes align with goals and objectives.
In the context of a warehouse, KPIs are quantifiable metrics that gauge the performance, efficiency, and effectiveness of various aspects of the logistical and operational processes.
Measuring your warehouse’s performance is crucial. KPIs empower decision-makers with real-time data allowing you to:
- integrate various processes,
- monitor trends,
- assess operational efficiency,
- identifying strengths and weaknesses,
- manage risks,
- enable resource optimization, and more.
In essence, warehouse KPIs transcend mere numerical metrics; they serve as a compass, driving continuous improvement and fostering a culture of efficiency within the warehouse ecosystem.
Selecting the Right KPIs for your Business
Although warehouses operate differently, most management KPIs are versatile and applicable across various warehouse types.
These metrics range from the straightforward, such as order fulfillment speed and inventory accuracy, to the more complex, including order cycle time, carrying costs, and labor productivity.
So how do you find the KPIs you actually need?
- Identify Business Objectives:
Start with a clear outline of your business goals. Defining your mission and objectives sets the stage for selecting KPIs that truly matter. - Assess Key Processes:
Focus on areas that have a direct impact on efficiency, customer satisfaction, and overall success. - Consider Industry Standards:
Explore industry benchmarks to gain insights into commonly used KPIs. This provides a foundation for comparison and ensures your metrics are relevant. - Engage Stakeholders:
Collaboration is key. Consult with warehouse managers, employees, and decision-makers to select KPIs that resonate with the operational realities of your warehouse. - Prioritize Metrics:
Prioritize KPIs based on their relevance to your business objectives. Focus on the most impactful metrics aligned with your strategic priorities.
The most important Key Performance Indicators (KPIs) for measuring warehouse efficiency often apply broadly across different industries and warehouse types.
15 Critical KPIs for Measuring Warehouse Efficiency
Here are some universally relevant KPIs and their basic formulas that provide valuable insights into warehouse efficiency:
- Order Fulfillment Speed: Gauge the speed at which customer orders are processed and fulfilled.
- Formula: (Total Orders Fulfilled) / (Total Time for Fulfillment)
- Example: If 500 orders were fulfilled in 20 hours, the Order Fulfillment Speed would be 500/20 = 25 orders per hour.
- Inventory Accuracy: Evaluate the precision of inventory records and the reliability of stock levels.
- Formula: (Book Inventory / Physical Inventory) x 100
- On-Time Delivery Rates: Assess the punctuality of delivering orders within the specified timeframe.
- Formula: (Total Number of Deliveries) / (Number of On-Time Deliveries) ×100
- Order Cycle Time: Measure the time taken from order placement to delivery.
- Formula: (Total Time for Order Processing) / (Number of Orders Processed)
- Carrying Costs: Evaluate the costs associated with holding and storing inventory.
- Formula: (Average Inventory Level) × (Carrying Cost per Unit)
- Labor Productivity: Assess the efficiency and output of labor resources, indicating workforce effectiveness.
- Formula: (Total Output) / (Total Labor Hours)
- Space Utilization: Measure the effective use of warehouse storage space.
- Formula: (Actual Storage Space Used) / (Total Available Storage Space) × 100
- Example: If 4000 square feet of storage space is used out of a total of 5000 square feet, the Space Utilization would be 4000/5000×100 = 80%.
- Return Rates: Evaluate the frequency and reasons for product returns.
- Formula: (Number of Returned Items) / (Total Items Shipped) × 100
- Pick and Pack Accuracy: Measure the accuracy of picking and packing processes, ensuring correct fulfillment of customer orders.
- Formula: (Number of Correctly Picked and Packed Orders) / (Total Number of Picked and Packed Orders) × 100
- Order Accuracy: Assess the accuracy of order processing.
- Formula: (Number of Correctly Processed Orders) / (Total Number of Processed Orders) × 100
- Turnover Rates: Evaluate how quickly inventory is sold and replenished.
- Formula: (Number of Units Sold) / (Average Inventory Level)
- Backorder Rates: Measure the frequency of items placed on backorder.
- Formula: (Number of Backordered Items) / (Total Number of Ordered Items) × 100
- Dock-to-Stock Time: Measure the time it takes for received goods to be made available for order fulfillment, optimizing inventory flow.
- Formula: (Time Taken for Goods to be Stocked)
- Example: If it takes 6 hours for received goods to be stocked, the Dock-to-Stock Time is 6 hours.
- Shipment Accuracy: Assesses the accuracy of shipped orders, including correct items and quantities, ensuring customer satisfaction.
- Formula: (Number of Accurate Shipments) / (Total Number of Shipments) × 100
- Resource Utilization: Measure the efficiency of resource usage, including labor, equipment, and technology.
- Formula: (Total Output or Productivity) / (Total Resource Input)
These KPIs provide a comprehensive view of warehouse efficiency by addressing key aspects of order fulfillment, inventory management, and operational processes.
While specific industries or warehouses may prioritize certain KPIs based on unique requirements, these universally applicable metrics are a solid foundation for assessing and optimizing warehouse efficiency.
Implementing Key Performance Indicators Successfully
With some thoughtful planning and strategic execution KPIs can transform your warehouse into a highly efficient and responsive operation, driving continuous improvement, optimizing resource utilization, and ultimately propelling it to the forefront of industry excellence.
Here are key strategies for ensuring effective KPI integration in your organization:
- Implement a KPI Tracking System:
- Invest in a robust KPI tracking system or software that allows for real-time monitoring and reporting. Accessibility and visibility are crucial for effective KPI management.
- Provide Training and Education:
- Ensure that employees at all levels understand the significance of KPIs and how they contribute to overall organizational success. Provide training on KPI usage, interpretation, and action planning.
- Set Realistic Targets:
- Establish realistic and achievable targets for each KPI. Unrealistic goals can lead to demotivation and may not accurately reflect the potential for improvement.
- Regular Monitoring and Review:
- Implement a regular cadence for monitoring and reviewing KPIs. Regular assessments allow for timely intervention and adjustments to strategies based on evolving business needs.
- Cascade KPIs Throughout the Organization:
- Ensure that KPIs are communicated and understood at all organizational levels. Cascading KPIs promotes a unified understanding of performance expectations.
- Establish a KPI Governance Structure:
- Create a governance structure that defines roles and responsibilities for KPI management. Clearly designate who is responsible for data collection, analysis, and reporting.
- Incorporate KPIs in Performance Reviews:
- Integrate KPIs into performance reviews and assessments. Linking individual and team performance to KPIs reinforces accountability and goal alignment.
- Adapt and Evolve:
- Regularly reassess and adapt your set of KPIs to align with changing business objectives and industry trends. Flexibility ensures ongoing relevance and effectiveness.
By implementing these strategies, organizations can establish a robust framework for successful KPI integration, ensuring that metrics are aligned with business goals and contribute meaningfully to overall performance improvement.
The Instrumental Role of Technology
Technology now plays a crucial role in the way businesses monitor, analyze, and leverage data to enhance operational efficiency. In can aid in providing real-time insights, automation, and advanced analytics to optimize warehouse performance.
Here’s how technology enhances the monitoring and analysis of KPIs:
- Automation of Data Collection:
- Role: Automated data collection from various sources within the warehouse.
- Enhancements: Automated systems, such as Warehouse Management Systems (WMS) and Internet of Things (IoT) devices, continuously capture data related to inventory levels, order processing times, and equipment utilization.
- Real-time Visibility:
- Role: Real-time monitoring of KPIs.
- Enhancements: With advanced sensors and tracking systems, warehouse managers can access up-to-the-minute data on key metrics. This real-time visibility allows for proactive decision-making and quick responses to changing conditions.
- Data Integration and Connectivity:
- Role: Seamless integration of data from various warehouse systems.
- Enhancements: Warehouse technologies integrate with Enterprise Resource Planning (ERP), Customer Relationship Management (CRM), and other business systems. This integration ensures a holistic view of operations and enables a comprehensive analysis of KPIs in the context of overall business goals.
- Mobile Applications:
- Role: Technology extends KPI monitoring capabilities to mobile devices.
- Enhancements: Mobile applications enable warehouse managers to access KPIs on-the-go. Whether in the warehouse or off-site, decision-makers can stay connected to real-time data.
- Cloud-Based Solutions:
- Role: Leverage cloud-based solutions for data storage and accessibility.
- Enhancements: Cloud platforms provide scalable and secure storage for vast amounts of data. Stakeholders can access KPIs from anywhere with an internet connection, facilitating collaboration and remote monitoring.
Integrating technology enhances the monitoring and analysis of KPIs and the overall efficiency and competitiveness of warehouse operations.
Metrics of Success
Optimizing warehouse operations is the key to long-term success for any business. The integration of warehouse KPIs, supported by innovative technologies, transforms warehouses into highly efficient and responsive operations.
Highlighting 15 critical KPIs, we’ve discussed universally relevant metrics and their formulas, offering a comprehensive view of warehouse performance. For a more in depth look at KPIs, the Warehousing Education and Research Council (WERC) recently presented findings from its annual DC Measures survey at its 46th Annual Conference. The study revealed a heightened focus on “the perfect order” among respondents, encompassing orders shipped on time, complete, damage-free, and with correct documentation, while also exploring the evolving role of environmental, social, and governance (ESG) initiatives in the distribution and logistics industry.
KPIs can serve as catalysts for continuous improvement, optimizing resource utilization, and propelling warehouses to the forefront of industry excellence. As technology continues to revolutionize warehouse operations, the marriage of KPIs and cutting-edge tools ensures that warehouses not only meet but continually exceed performance expectations, fostering a culture of sustained success in the modern business era.