Insights from Richard Coppola on Current Challenges and Best Practices
In this next edition of our interview series, Richard Coppola, an expert in shelf stable food commodities, offers a comprehensive look at the unique challenges and best practices in this domain. Our discussion spanned various critical areas, including the distinguishing features of these commodities, the impact of global supply chain dynamics, and the essential strategies for managing risks and operational challenges.
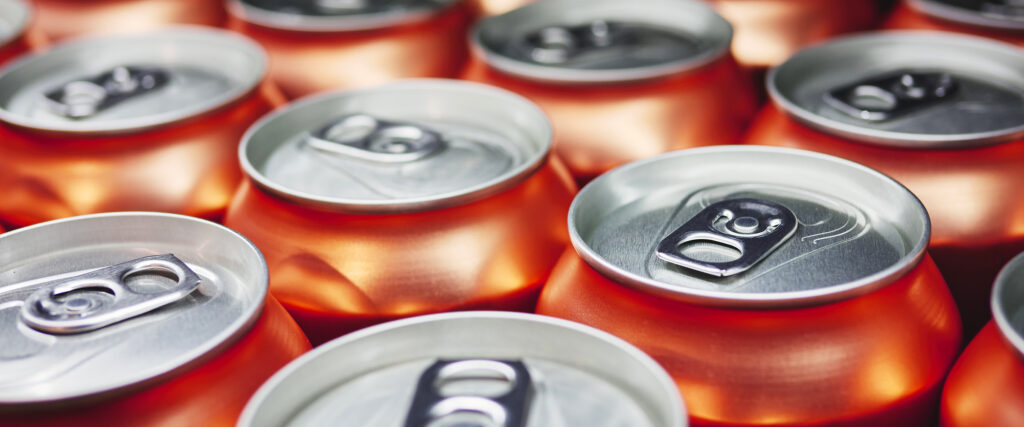
Welcome back, Richard. We’re excited to dive into a new topic with you today. As someone with extensive experience in the logistics and supply chain sector, your insights on shelf-stable food commodities will be invaluable.
First, can you give us an overview on shelf stable food commodities and how they differ from the candy and confectionaries we spoke about in our first conversation?
Shelf-stable food commodities are distinct because they require no preparation before consumption. You can walk into a warehouse, open a box, and eat the contents without any further steps. This contrasts with items that require cooking or refrigeration.
Shelf-stable products, such as canned goods, dried fruits, and certain packaged snacks, may or may not require temperature control. At East Coast Warehouse, we cater to both ambient and temperature-controlled storage, ensuring that the challenges for both are addressed similarly.
What are some of the recent challenges in the global supply chain, and how do they affect shelf-stable commodities?
The global supply chain has seen a lot of disruptions over the past five years, starting just before COVID. These disruptions affect everything, whether you’re importing canned goods that don’t need temperature control or chocolates that do. We’re all dealing with the same issues—geopolitical instability, economic fluctuations, and extreme weather events. Take the Panama Canal, for example. They had to limit the number of vessels passing through because of a lack of rain. Then there’s the rising cost of raw materials, which puts pressure on everyone in the supply chain.
And now, cybersecurity is a big threat. One attack can bring the whole supply chain to a halt. We’re also seeing more frequent extreme weather events, which used to be “once in a century” but are happening a lot more often now. It’s really about being proactive with risk management and building these considerations into your supply chain model.
Given these challenges, what strategies do you recommend for managing risks associated with shelf-stable commodities?
In today’s environment, choosing the right supply chain partners is more critical than ever. Misalignment can lead to significant disruptions, impacting your ability to serve customers and achieve economic goals. For example, the ILA labor contract, which expires at the end of September, could lead to a strike affecting around 100 ports if not successfully negotiated. This would have profound economic consequences.
At East Coast Warehouse, we’ve been proactively communicating with our customers about this potential disruption since January. One strategy we’ve employed is building in some insurance protection by bringing products in earlier to have safety stock on hand, minimizing the risk of delays.
What are some unique operational challenges East Coast Warehouse faces when handling these commodities?
One of the biggest challenges we face is port congestion. If the port isn’t operating efficiently, it can cause major delays, and that’s a problem, especially when you have containers that are floor-loaded with multiple SKUs and lot codes. It takes more time and money to unload, sort, and store these products. For example, if a customer’s seasonal products arrive all at once, we might have containers stacked up, all needing to be processed quickly. It’s about managing that flow efficiently and being aware of the potential delays and costs involved.
How does East Coast Warehouse approach inventory management and regulatory requirements?
Communication with our clients is key. We like to have an ongoing dialogue, getting forecasts and updates on what’s coming in so we can plan properly. We ask our customers to notify us at least 48 hours in advance before their products hit the port.
On the regulatory side, we operate an SQF-certified warehouse, which is the highest standard in the U.S. for storing and transporting food. We have strict guidelines to make sure that the products coming in meet all the necessary requirements and that there’s no risk of contamination or infestation.
Can you elaborate on the role of technology in managing these commodities?
Technology is crucial, especially now with all the challenges in the supply chain. We give our customers unrestricted access to their inventory data through our online management system, so they have complete visibility over what’s in the warehouse, what’s coming in, and what can be shipped out. This transparency helps them make informed decisions and avoid overcommitting to their customers. Setting the right expectations and making sure everyone is on the same page ensures smoother operations.
What are the best practices for packaging and handling shelf-stable commodities?
The most important thing is to ensure that the product’s integrity is maintained from the assembly line to the retail shelf. We’ve seen situations where rough seas during transit compress the boxes at the bottom of a container, damaging the product. That’s why it’s essential to choose the right packaging materials, like a heavier gauge cardboard.
During the onboarding process, we discuss these best practices with our customers, but ultimately, the packaging decisions are up to them. We just want to make sure they’re aware of the risks and how to mitigate them.
How does East Coast Warehouse manage transportation logistics for these commodities?
We offer a range of delivery options, from less-than-truckload (LTL) to full truckload (TL) services, covering the entire continental U.S. By integrating drayage, warehousing, and final-mile delivery, we reduce the chances of something falling through the cracks. If you’re relying on multiple vendors, there’s always a risk that one might not meet the same standards.
We’ve seen cases where outside truckers show up with a dirty truck or a damaged trailer, which can ruin a shipment. By keeping everything in-house, we maintain control over the entire process and ensure the product arrives in perfect condition.
Are there any trends in the future of shelf-stable food commodities?
One trend I’m seeing is the growing importance of being close to the port. Having your warehouse near a major port is crucial for a resilient supply chain. This proximity reduces transit times and lowers the risk of delays. Another trend is the shift towards finding partners who can offer end-to-end solutions. Importers realize that by streamlining their operations with a single, capable partner like East Coast Warehouse, they can reduce complexity and increase efficiency.
Sustainability is also becoming more important, especially for our European clients who are increasingly interested in our environmental initiatives. Our warehouses use LED motion sensor lighting and solar panels, which help reduce our carbon footprint. Being located near the port also lowers emissions since our trucks don’t have to travel far. It’s all about making the supply chain as smooth and reliable as possible.
Conclusion
Richard highlighted the importance of selecting the right supply chain partners, understanding and navigating global challenges, and adopting best practices for managing shelf stable food commodities.
Proactive planning, transparent communication, and leveraging technology are key strategies for successfully managing the complexities of the modern supply chain.
As we move forward, these insights will prove invaluable in ensuring the continuous availability and quality of shelf stable food products.