Some parts of the supply chain are flashy—global shipping lanes, robotics in mega-warehouses, AI-driven demand forecasts.
Then there’s drayage.
It’s not flashy. But it’s critical. Drayage is the short-haul movement that gets containers from the port to a warehouse or distribution center. When it runs smoothly, you hardly notice it. When it doesn’t, everything grinds to a halt—inventory sits idle, timelines slip, and costs start to climb.
📊 And business is only getting busier. According to a 2025 report from Technavio, the global drayage services market is projected to grow by $2.46 billion between 2025 and 2029, a clear signal that short-distance freight movement is becoming even more essential to keeping goods flowing and customers happy.
Too often, drayage and warehousing are treated as separate functions. They’re managed by different vendors, run on different systems, and operate with different priorities. The result? Missed opportunities, duplicated effort, and plenty of room for error.
But when drayage and warehousing are aligned—ideally coordinated by a single provider or through a tightly integrated partnership—everything changes.
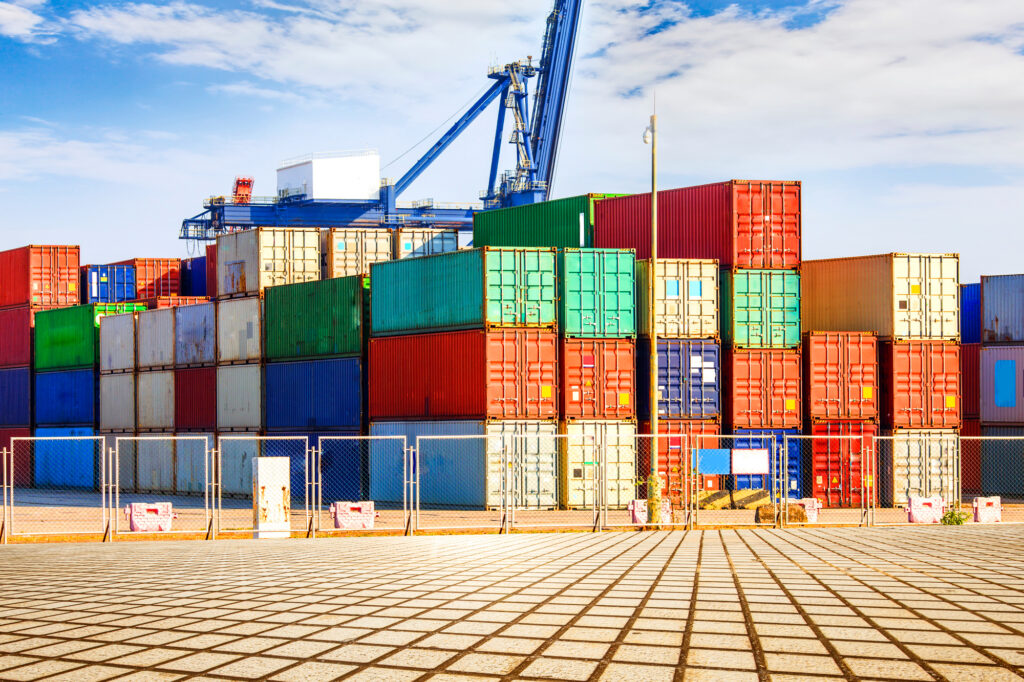
Drayage and Warehousing: Why This Connection Matters
Drayage is a sprint. Warehousing is a marathon. One handles the pressure of port congestion, tight windows, and rising fuel costs. The other focuses on inventory control, throughput, and last-mile readiness. Alone, each has its challenges. Together, they create a system that’s greater than the sum of its parts.
Here’s what happens when the two work in sync:
1. Fewer Delays, Fewer Fees
When a container lingers at the port too long, it triggers demurrage fees. When a truck is forced to wait at the warehouse gate, detention charges follow.
These costs add up quickly—but they’re often avoidable. If drayage and warehousing teams are aligned on schedules, volumes, and receiving capacity, they can plan for efficient handoffs. That means no waiting, no bottlenecks, and far fewer surprise invoices.
2. Improved Visibility and Communication (And Why It’s a Game-Changer)
Visibility is the beating heart of modern logistics. Without it, your team is reacting instead of planning—and in today’s supply chain environment, reacting late can mean losing customers, not just money.
When drayage and warehousing operate independently, communication tends to fall into one of two camps: fragmented or delayed. A driver gets held up at the port, but the warehouse doesn’t hear about it until they’ve already scheduled a team for unloading. A container is flagged for inspection, but there’s no real-time update to adjust delivery timelines downstream. Multiply those scenarios across dozens—or hundreds—of shipments, and you’re running a supply chain in the dark.
Now imagine this instead:
- Your warehouse team sees real-time updates on inbound containers and can shift labor allocation accordingly.
- Your drayage partner has visibility into warehouse capacity and congestion, so trucks aren’t dispatched into logjams.
- Your customer service team has access to accurate ETAs and can proactively communicate with clients—no guessing, no scrambling.
This isn’t just about smoother handoffs. It’s about being able to forecast problems before they arise. When both sides operate on shared platforms or integrated systems, you build a feedback loop that improves decision-making across the board:
- Labor planning becomes more efficient. No more paying overtime because a truck showed up late and unannounced.
- Yard and dock management becomes smarter. You avoid bottlenecks, overbooking, and underutilization.
- Customer satisfaction improves. When deliveries hit consistently and communication is clear, trust builds.
On a strategic level, this visibility becomes a competitive edge. Retailers and manufacturers can adjust inventory strategies based on accurate inbound data. Logistics managers can model cost scenarios with up-to-date movement metrics. Even your finance team benefits—fewer surprises mean more predictable spending.
In short, communication and visibility are the key to a supply chain that runs efficiently, scales easily, and keeps customers happy.
3. Faster Turnaround, Smarter Fulfilment
Warehouses that receive real-time updates from drayage providers can prepare space and labor ahead of arrival. Containers can be prioritized based on urgency. Inventory can be processed and moved faster, which shortens the time from port to end customer. For businesses with tight delivery windows or high-volume operations, this speed isn’t just convenient—it’s essential.
4. Better Use of Resources
When drayage and warehousing are planned together, you avoid duplication of effort. That might mean fewer truckloads, less re-handling of goods, and more efficient use of warehouse labor. These efficiencies translate directly to cost savings and better ROI across the supply chain.
High-Pressure Ports Make Integration Even More Valuable
If you’re operating near major U.S. ports like New Jersey, Philadelphia, or Baltimore, you already know the stakes are high.
These are busy, high-volume hubs where capacity is tight, windows are short, and demand is constant. In these environments, the margin for error shrinks—and the value of coordination skyrockets.
A nearby warehouse that’s also managing your drayage operations can be a strategic advantage. It shortens travel time, reduces fuel costs, and improves scheduling control. Some providers even offer drayage as an in-house service, giving you a single point of contact, unified systems, and a much smoother flow of goods.
By managing both the transport and storage components of the operation, they offer more control over schedules, fewer handoffs, and quicker throughput—especially in high-pressure hubs like these.
What Strategic Supply Chains Are Doing Differently
The most agile supply chains today don’t treat drayage and warehousing as isolated transactions. They approach them as linked stages of a unified operation. That shift in mindset opens the door to:
- Predictable delivery timelines
- Lower total landed cost
- Higher customer satisfaction
- Stronger supply chain resilience
In fact, a 2024 report by KPMG highlights that implementing AI-enabled, low-touch planning in supply chains can enhance predictability, improve return on equity by 2 to 4 percentage points, and increase gross margins by 1 to 3 percent. This demonstrates the tangible financial benefits of adopting integrated and technologically advanced logistics strategies.
In other words, it’s not just about moving goods from A to B. It’s about creating a process that’s coordinated, intelligent, and designed for the pace of modern commerce.
Final Thoughts
Every supply chain has pressure points. But many of the most common ones—delays at the port, warehouse congestion, missed delivery deadlines—can be traced back to a lack of coordination between drayage and warehousing.
The fix isn’t complicated. It’s strategic alignment. It’s choosing partners who think beyond the truckload or the storage rack. It’s investing in systems and relationships that connect the dots—so your supply chain runs like a system, not a series of disconnected steps.
If your drayage and warehousing partners aren’t working together, your supply chain is working harder than it needs to.
Now’s the time to change that.