In this edition of our interview series, we spoke with Steve Banasiak, Director of Business Development at East Coast Warehouse. Steve shared insights on the Centralized Examination Station (CES) operations, the challenges of managing CES, and the critical role they play in ensuring the safety and compliance of cargo entering and leaving the United States.
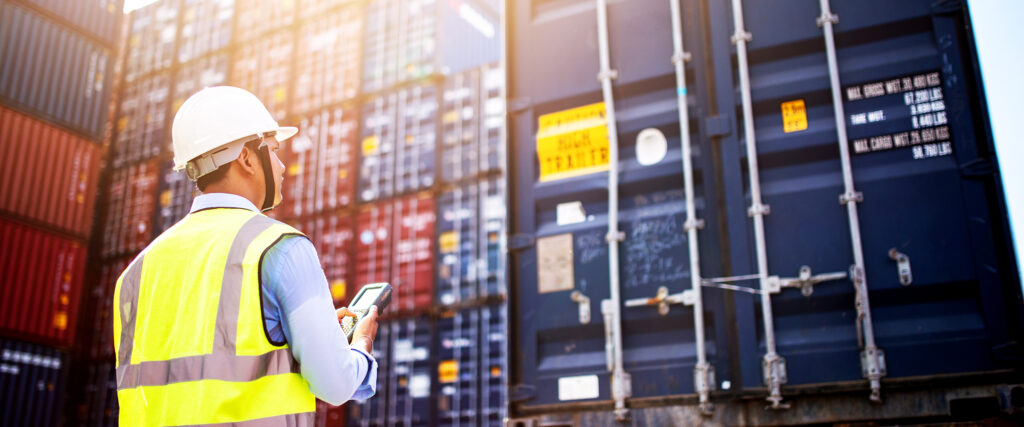
Steve, could you start by telling us a bit about your role and responsibilities at East Coast Warehouse?
I’m the Director of Business Development here at East Coast Warehouse, focusing on our CES product. We’ve been acting as a CES for 30 years. Essentially, we work with Customs and Border Protection (CBP) to assist them during their cargo inspections. We pick up containers from the terminal, bring them to our facility, and after customs completes the inspections, we reload the cargo back into containers for further transportation.
What does “safe cargo” mean, and what makes certain cargo unsafe?
When we talk about “safe cargo,” we’re referring to the types of goods that meet all regulatory standards and pose no threat to public safety, health, or intellectual property rights. Different customs exam teams focus on various aspects of cargo safety. CBP exam teams consist of Enforcement, Agriculture and Trade, and other government agencies such as the Consumer Product Safety Commission (CPSC).
What types of cargo do you typically handle at your CES facilities?
While our public warehouse deals with a lot of confectionery and beverages, the CES section can handle anything from fruits and food products to used shoes and machinery. It all depends on what customs targets for inspection.
How has the demand for CES services evolved over the past few years?
The funny thing about being a CES operator is that the business volume isn’t guaranteed. Demand fluctuates based on customs’ focus at the time. Over my 14 years in this role, I’ve seen significant changes in exam volumes driven by various factors.
For example, agriculture exams are highly seasonal. During the Cold Treatment inspection period from November to April, cargo must stay at a specific temperature to ensure pests are eradicated. This is part of a program with the USDA, aiming to prevent pests from entering the country and affecting domestic crops.
Another area being scrutinized by CBP is forced labor. This focus has increased the number of containers we handle for exams.
What recent technological advancements have impacted CES operations?
The technology currently being used is customs’ ACE system, which helps us receive information about containers in real-time. This visibility allows us to pick up and present containers to customs more efficiently, reducing turnaround times. Additionally, our web tools enable the community to track the status of containers, ensuring a smooth process from pickup to release.
The implementation of ACE has significantly enhanced our operations. Before 2012, we relied on customs inspectors to inform us about containers needing inspection. This manual process often led to delays. Now, with ACE, we receive the same real-time data as customs brokers and steamship lines. This synchronized visibility allows us to dispatch containers more promptly, shortening turnaround times and making cargo available to clients much faster.
How does your unique location and operational setup enhance your efficiency in container handling?
Our strategic location in New York/New Jersey, where we are the only CES operator on port property, gives us a competitive advantage. Proximity to the terminals allows us to pick up containers quickly, and our experience and strong relationships with CBP and the shipping community further enhance our efficiency. In addition, the average time for a trucker to come into our facility and pick up a container once it is fully released is about 15 to 20 minutes, compared to much longer wait times at other facilities. This efficiency is a key reason why steamship lines and customs brokers prefer to designate us for exams.
What are the biggest challenges you face in managing CES operations?
One major challenge is dealing with terminal congestion. At East Coast CES we are focused on picking up containers within 24-48 hours of CBP placing the hold in ACE, but during times of port congestion this is very challenging. Most containers are picked up on a first-in, first out basis with reefer and Cold Treatment containers taking priority due to their perishable nature.
We understand that containers selected for an exam instantly become urgent to the customer even if they weren’t initially. Our job is to work closely with customs and the community to ensure that all containers are picked up from the terminal, presented to CBP and available to the community after the exam as quickly as possible.
How do CES operations integrate with East Coast Warehouse’s other services?
While CES operations are mostly independent, there is occasional coordination needed when a warehouse account gets selected for an exam. Our drayage services handle container pickups for CES, warehouse accounts, and direct customers, with CES containers often taking priority due to the critical nature of their inspections.
Are there measures in place to handle high-risk or sensitive cargo that requires special attention during inspections?
Yes, we have procedures for handling hazardous cargo and high-risk containers flagged by customs. We also accommodate importers participating in the Customs-Trade Partnership Against Terrorism (C-TPAT) program, providing front-of-line privileges for vetted importers.
What is the importance of maintaining strong relationships with customs and the community?
I belong to several associations in the different ports where we operate. This involvement helps me stay close with both customs brokers and steamship lines. I attend various meetings to stay informed about new regulations and programs that brokers and steamship lines are dealing with. This involvement allows me to understand their challenges and maintain credibility when working with these parties or seeking their designations.
By being visible and active in these associations, I ensure we continue to provide quick turn times and effective service to the community.
What are some common misconceptions about the CES process?
One of the most common misconceptions is that we, as the CES operator, are the ones choosing containers for inspection. In reality, it is Customs and Border Protection (CBP) that selects the containers. Our job is simply to make sure that we are picking up containers and presenting them to CBP as quickly as possible for inspection. After that, we make sure that containers are quickly available to the community once released by CBP.
Another misconception is that we have special access at terminals to pick up containers more quickly. In truth, we wait in line like everyone else. If there is a long wait time at the terminal, we experience the same delays as other truckers. There are no special gates or expedited processes for us simply because we are handling containers for customs.
Does it cost importers money when their containers are selected for inspection?
Yes, while customs doesn’t charge for the inspection itself, importers incur costs related to our exam fees, including drayage, facility, and inspection fees. These fees are filed with customs and are publicly available on our website. The customs broker usually handles these charges on behalf of the importer.
Do you have any specific examples of success stories where your CES operations benefited clients?
One notable example is our work with imported fruits. Customs Brokers and Importers rely on us to ensure quick processing so the fruit can reach the market at the highest price. We’ve received positive feedback from brokers about our efficiency during the last fruit season, highlighting our focus on quick turn times and priority handling.
We hope you enjoyed this interview with Steve Banasiak and learned more about the crucial role of Centralized Examination Stations in the logistics and supply chain industry. East Coast Warehouse continues to be a trusted partner, ensuring the safety and compliance of cargo through efficient and transparent operations.